TATA Steel’s Quick Shutdown Boosts Mill Efficiency
The following case study focuses on the implementation of CCPM for the finishing mill upgrade project; a $90 million endeavor aimed at increasing the output of TATA Steel’s finishing mill from 3.25 million tons to 4 million tons per annum.
Case Summary
- 01
Challenges
- Stubborn foundation bolts threatening timeline
- Critical motor alignment under severe time pressure
- Single crane bottleneck risking project flow
- 500+ interdependent tasks demanding precise coordination
- Unforeseen disruptions from unrelated project
- 02
Our Work
- Single crane optimization through strict allocation rules
- Focus-&-Finish batches managing 500+ interdependent tasks
- Swift recalibration addressing unexpected pipeline project impact
- 03
Results
- Completed in 8.8 days, against the target of 11 days
- Saved $4.4 million in potential revenue loss
Business Challenge
The Finishing Mill Upgrade at TATA Steel posed significant challenges that threatened to derail its ambitious goals and critical timeline. The project aimed to replace 45-ton gearboxes and a 60-ton motor within an 11-day shutdown window, alongside installing a third reheating furnace and upgrading the roughing and finishing mills. This intricate task demanded seamless coordination across diverse disciplines and international suppliers, including TECO Westinghouse (UK), SMS Demag (Germany), and Converteam (US).
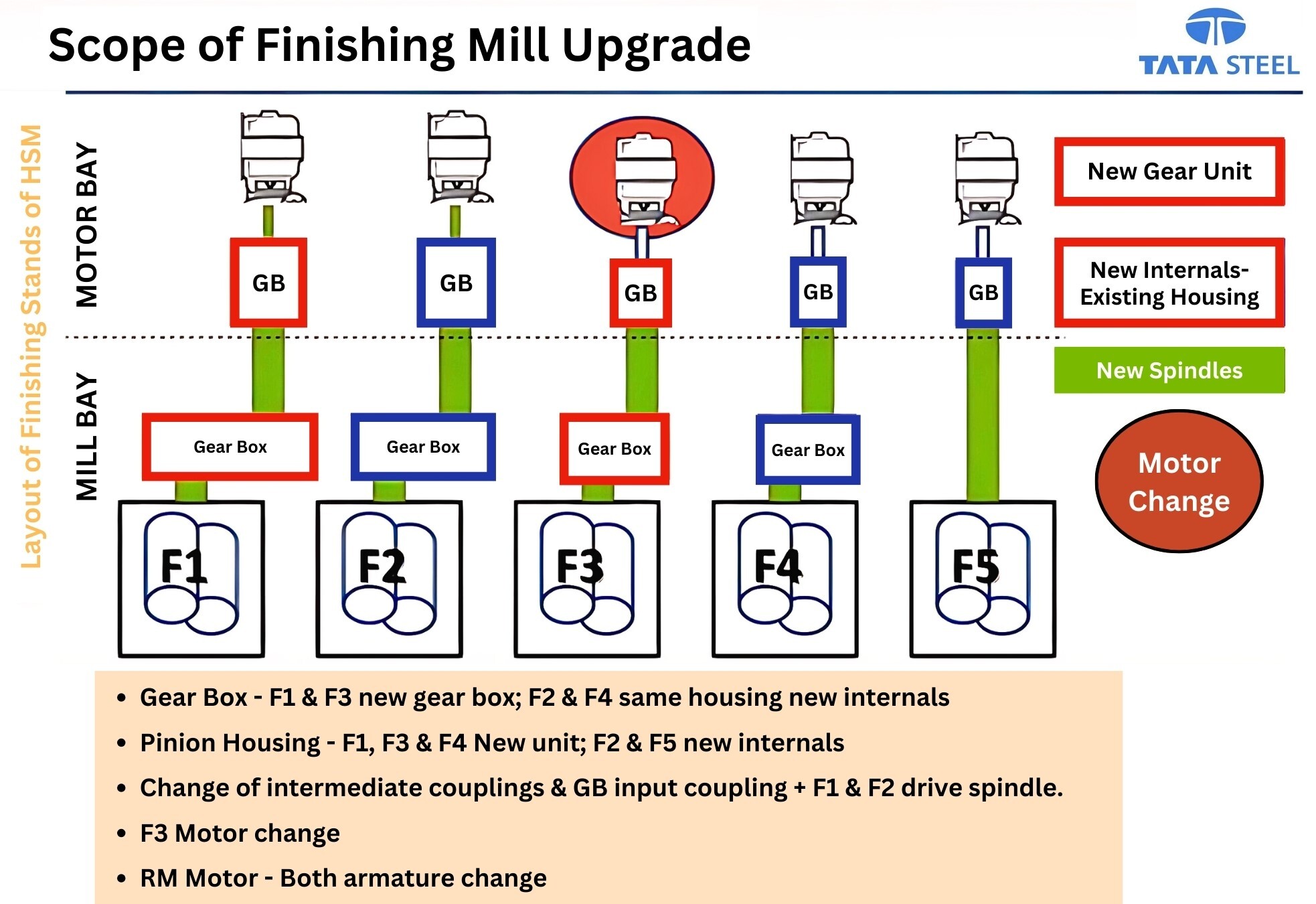
Our Solution
The CCPM implementation began with a comprehensive feasibility study. By testing the replacement of the F2 motor, the team identified potential pitfalls and developed pre-emptive strategies that involved calculating precise time requirements for each task to ensure the overall timeline was feasible. High-risk areas were identified, and contingency plans were formulated to address potential issues quickly. The entire replacement process was simulated to identify and mitigate logistical challenges. Clear communication protocols were established for rapid issue resolution and decision-making, resulting in a 25% reduction in project risks.
Resource allocation was optimized to ensure that key personnel and equipment were available when needed. Managing crane usage was a significant challenge, as the available crane operated at 71% of its capacity, which was exceptionally high. With only one crane capable of fitting inside the mill area, obtaining another crane was not feasible. Therefore, we implemented a staggered scheduling system to distribute the load and avoid bottlenecks evenly. Crane usage and resource allocation rules were enforced to prevent delays, ensuring the crane was available for critical tasks at the right moments. This approach was pivotal in maintaining project momentum and efficiency.
Perhaps most crucially, the CCPM methodology facilitated rapid decision-making. Strict rules were established for work release and task sequencing, achieving a remarkable 95% adherence rate. Escalation of issues to top management ensured problems were resolved promptly, minimizing delays. For example, an unexpected issue with a pipeline project at Tower 4 was resolved by redesigning the foundation and relocating worker restrooms, thanks to swift intervention and collaboration with the workers' union. In another instance, a quick decision on repurposing existing foundation bolts saved 48+ hours. This agility proved invaluable when unexpected challenges arose, such as difficulties with foundation bolts and unforeseen obstacles from an unrelated gas pipeline project.
Key Challenges and Overcoming Them
1. Resource Coordination: Optimizing the use of the only crane capable of operating within the confined mill area was critical.
Strict rules governing crane usage and optimized resource allocation were implemented to enhance efficiency. By staggering crane operations and enforcing guidelines to minimize downtime, the project maintained a steady workflow, crucial for meeting production targets within the shutdown window.
2. Task Interdependencies: Managing over 500 concurrent activities required meticulous planning to avoid conflicts and ensure a synchronized workflow.
Tasks were grouped into 'Focus-&-Finish' batches, eliminating the need for continuous coordination. This strategy allowed teams to concentrate on specific deliverables with clear objectives. Proactive management techniques and clear communication channels ensured that potential conflicts were minimized, fostering uninterrupted progress across different phases.
3. Foundation Bolts: Old foundation bolts for the gearboxes were difficult to remove, threatening project timelines.
Quick decisions and rigorous testing validated the reuse of existing foundation bolts. This proactive approach saved significant time and avoided delays associated with extensive foundational modifications, ensuring the project stayed on track without compromising structural integrity.
4. Motor Replacement: Aligning and replacing the F2 and F3 motors within a stringent 65-hour timeframe was logistically complex.
Precision alignment and timely installation of the F2 and F3 motors were achieved through meticulous planning and execution. Adherence to a tight schedule ensured that critical dependencies were met, enabling seamless integration into the upgraded mill system.
These strategies underscored our commitment to overcoming complex challenges through proactive management, meticulous coordination, and decisive action, ultimately achieving the project's objectives efficiently and effectively.
Results
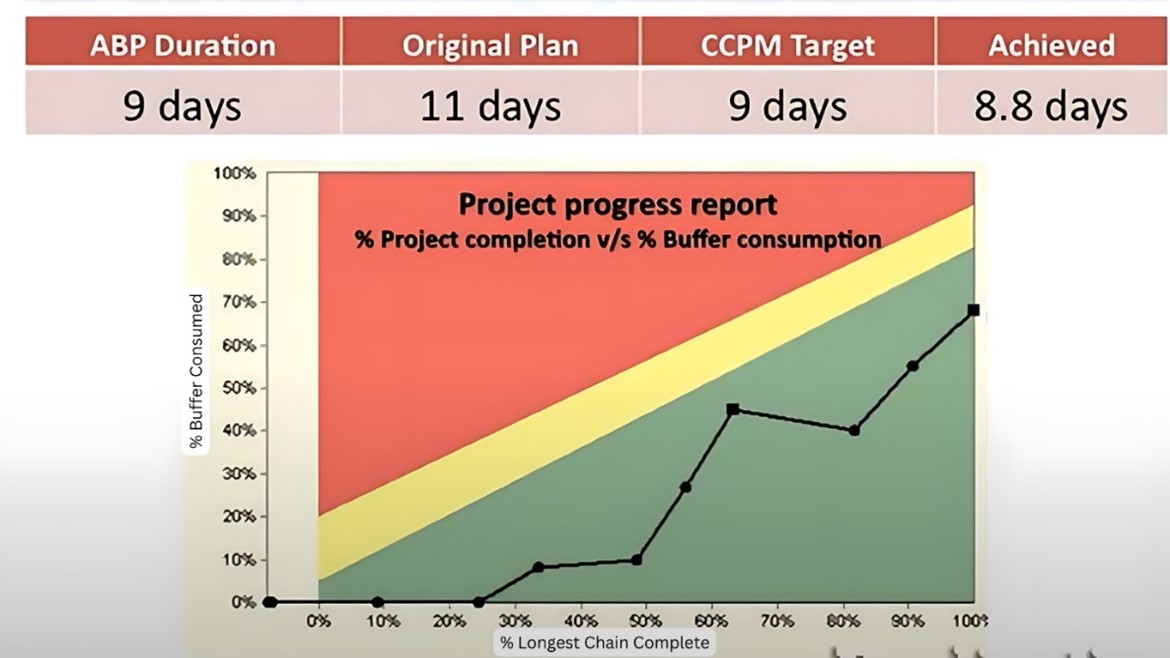
Conclusion
The recent upgrade of the finishing mill at Tata Steel showcases the powerful impact of Critical Chain Project Management (CCPM). Implementing the 'Focus & Finish' approach and addressing the critical bottleneck of crane usage, Tata Steel completed the project in just 8.8 days. This achievement exceeded the 11-day target and outperformed the previous 14-day benchmark, highlighting the effectiveness of identifying and resolving the right bottleneck over random widespread firefighting.
We needed to complete the project in 11 days against baseline performance of 15 days. Operations team had to be onboarded during the same time. We were able to complete Hot Strip Mill shutdown in 8.8 days against plan of 11 days.
Mr. Sudipto Sarkar
Contact us to find out more
Our Customer Service Teams have hundreds of Industry specific studies to draw from ... get in touch if you want to see something specific to your needs, or simply explore how we can deliver Radical Results for you.
Schedule a ‘Top-to-Top’ discussion with one of Realization’s
‘Radical Thinking Officers’.
Set-up a Discussion
Share your contacts and we will set up a ‘Top-to-Top’ meet.